E se fossero gli oggetti, o meglio, i componenti di parti strutturali di aerei, treni e auto a dire in quale stato si trovano e se necessitano di riparazioni o sostituzioni? Beh, di certo saliremmo su quei veicoli con maggior serenità! Ebbene, questa ipotesi non è tanto lontana dalla realtà, grazie alla ricerca nel campo dell’Ingegneria dell’Innovazione del Prodotto.
A rendere presto possibile questa importante innovazione dei prodotti sono (anche) gli studi condotti dal gruppo di ricerca sui materiali compositi del Dipartimento di Tecnica e Gestione dei Sistemi Industriali (DTG). Il Team è composto dai professori Marino Quaresimin, Direttore di Dipartimento e docente di Progettazione con Materiali compositi, Michele Zappalorto, Presidente del corso di Ingegneria dell’Innovazione del Prodotto e docente di Meccanica dei Materiali, e Paolo Andrea Carraro, docente del corso Metodi di Progettazione Meccanica alla Laurea Magistrale in Ingegneria dell’Innovazione del Prodotto.
Da qualche anno, infatti, presso i laboratori di San Nicola e delle Barche, il gruppo di Materiali Compositi del DTG sta lavorando allo sviluppo di materiali in grado di automonitorarsi, rivoluzionando così il modo di fare verifiche e manutenzione su prodotti come auto, aerei e turbine eoliche.
Materiali intelligenti e autonomi: dal laboratorio al loro impatto sulla vita di ciascuno
Il campo di indagine è quello del monitoraggio strutturale, e i settori di applicazione sono molti. Dal mondo dei trasporti (dalle auto all’aerospazio), al mondo dello svago con biciclette, caschi, sci e racchette, fino al mondo dell’automazione industriale e delle energie sostenibili.
“I materiali compositi sono sempre più utilizzati nella realizzazione di componenti strutturali e vantano un larghissimo impiego, ma al tempo stesso sono delicati perché si danneggiano facilmente, con microfessurazioni che però non sono visibili ad occhio nudo. Dunque, sono ancora più rischiose, specie se si tratta di componenti legati alla sicurezza o deputati al corretto funzionamento del mezzo, come nel caso di cerchi in composito per le auto o parti di aerei”, spiega il professor Zappalorto.
La conoscenza dello stato di integrità di questi componenti durante la loro vita attualmente viene spesso affidato a ispezioni periodiche programmate. L’innovazione messa in atto dall’utilizzo di questi materiali intelligenti permetterebbe un monitoraggio continuo nel tempo, con enormi benefici in termini di sicurezza, affidabilità e costi, passando da una manutenzione preventiva ad una condizionale.
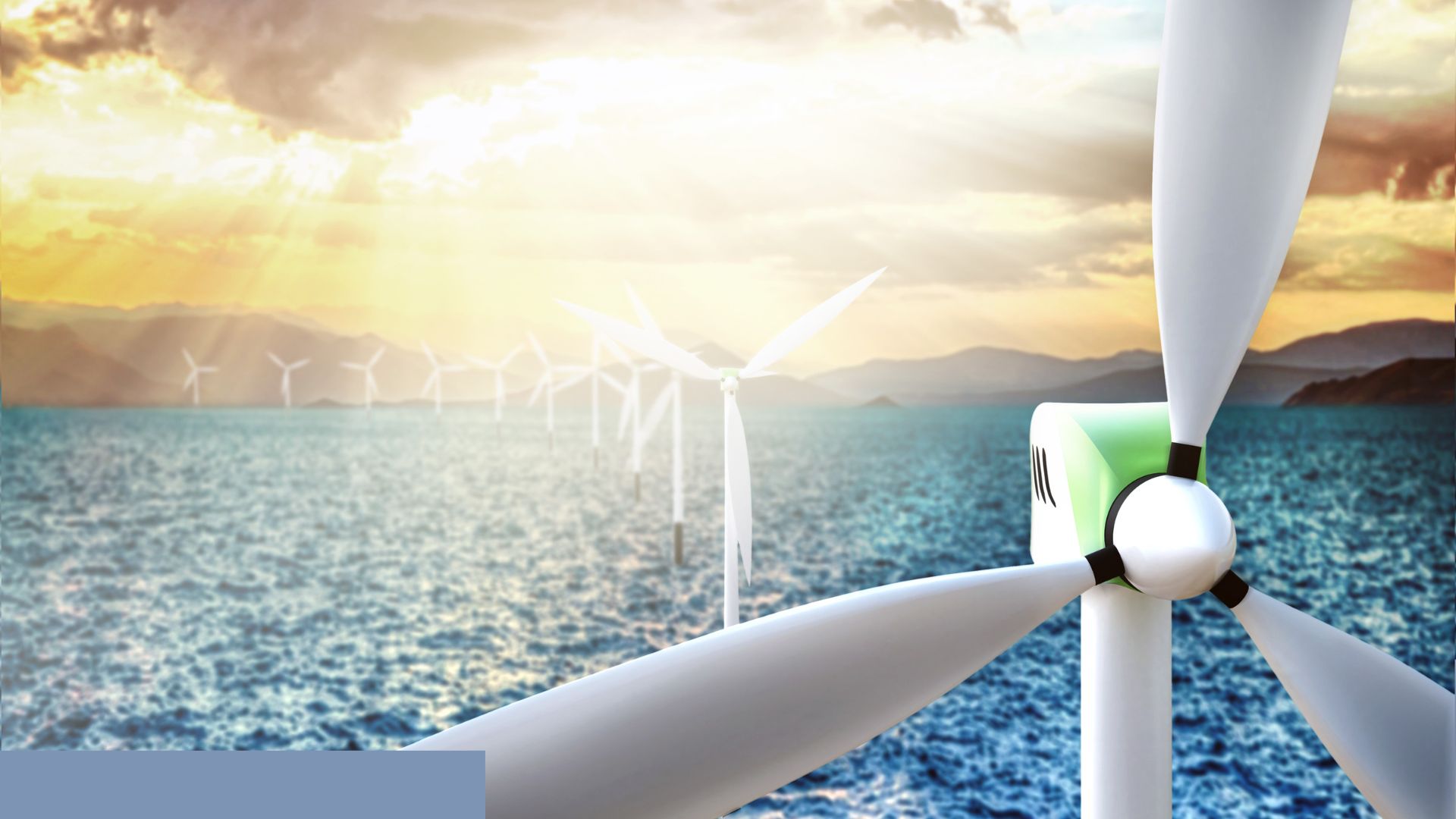
Dalle proprietà intrinseche dei materiali al monitoraggio autonomo
Il duplice obiettivo di garantire la sicurezza, per il prodotto e per l’utente, e di allungare la durata dei materiali in un’ottica di sostenibilità e riduzione dei rifiuti, ha dato il via alla ricerca.
“A questo scopo nascono i metodi elettrici per il monitoraggio strutturale, efficaci per individuare la presenza di danno in strutture in materiale composito elettricamente conduttivo (come ad es. in fibra di carbonio, CFRP, o con matrici nano-modificate) – spiega il Prof. Quaresimin -. Questi metodi si basano su semplici misure elettriche effettuate con appositi elettrodi posizionati all’interno di un componente o sulla sua superficie. L’energia elettrica necessaria può anche essere ottenuta in modo efficiente sfruttando le proprietà termoelettriche intrinseche dei materiali compositi”.
Lo studio condotto nei laboratori di Ingegneria dell’Innovazione del Prodotto
Da alcuni anni, quindi, nei laboratori del DTG si sta lavorando su due fronti. Da una parte allo sviluppo di materiali, modelli e metodi per il monitoraggio strutturale con metodi elettrici di componenti in composito. Dall’altra, alla caratterizzazione, modellazione e applicazione delle proprietà termoelettriche di tali materiali. “In un componente realizzato in materiale composito conduttivo, la comparsa di un danno interrompe il network elettrico e causa quindi un aumento irreversibile della resistività apparente del materiale, facilmente misurabile e utilizzabile come indicatore di danno” , prosegue il professor Zappalorto.
In altre parole, quando nel materiale del componente si verifica una interruzione del passaggio elettrico, significa che è presente un deterioramento o un danneggiamento, come ad esempio delaminazioni e rottura di fibre. Misurando quindi la variazione di resistenza elettrica del componente, con l’approccio sviluppato dai tre docenti del corso di Laurea in Ingegneria dell’Innovazione del Prodotto, è possibile quindi “interrogare” il materiale e rilevare la presenza di una rottura.
Il tutto può essere reso ancora più efficiente e sostenibile utilizzando le proprietà termoelettriche dei materiali compositi, che possono essere ottimizzate grazie ai modelli matematici innovativi sviluppati dallo stesso team nell’ambito del progetto HARVEST, un progetto Europeo triennale che il DTG ha svolto in collaborazione con altri centri di eccellenza ed aziende del settore aeronautico, tra cui anche AIRBUS.
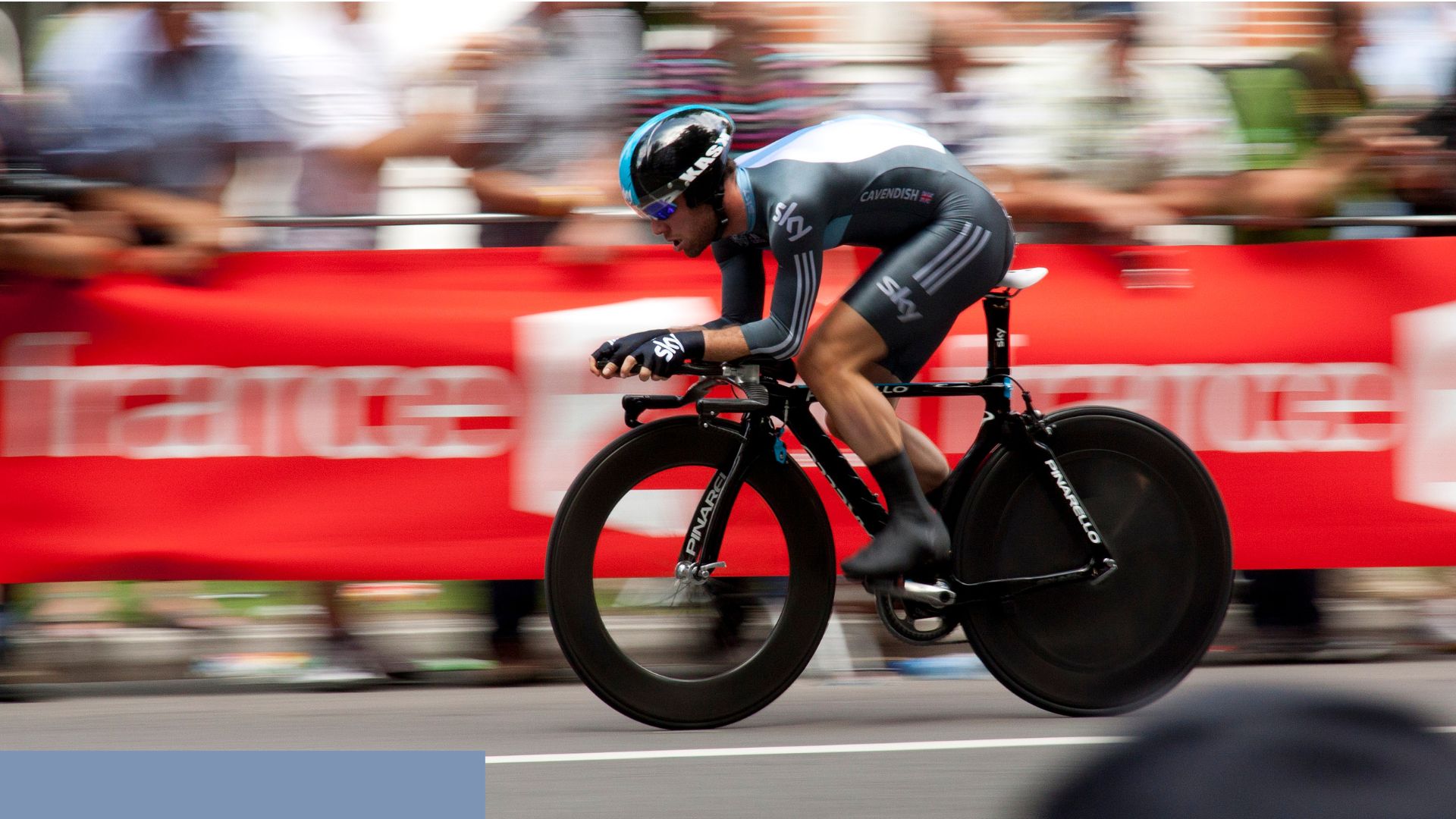
Ingegneria dell’innovazione del prodotto: nuove tecnologie per la sicurezza
Come primo passo verso metodologie efficienti per il monitoraggio strutturale, i membri del gruppo di ricerca sui Materiali Compositi, e docenti di Ingegneria dell’Innovazione del Prodotto, hanno sviluppato dei modelli analitici per stimare la correlazione tra i due eventi (interruzione elettrica-danno). Hanno così ottenuto una correlazione diretta tra l’aumento di resistenza elettrica e la diminuzione di rigidezza del materiale, causata appunto dal guasto. Ciò ha permesso di confermare la validità del sistema di monitoraggio per la presenza di un danno nel materiale e anche la possibilità di stimarne la severità.
Ecco dimostrato che, con l’utilizzo di materiali intelligenti ed autonomi nella realizzazione di prodotti innovativi come componenti essenziali di aerei, auto e macchine industriali, e molto altro ancora, il segnale dell’esistenza di un danno verrà inviato autonomamente dal materiale stesso. La tecnica di monitoraggio utilizzata è ancora più attrattiva per la nascita di una nuova generazione di strutture in composito intelligenti e autonome per applicazioni aerospaziali, grazie alla possibilità di sfruttare le proprietà termoelettriche dei compositi.
